Research Result Summaries
Objective: To ensure satisfactory circuit breaker life cycle performance research tasks in this project are designed to:
- Help utilities better understand circuit breaker operating stresses, underlying failure modes, and degradation rates
- Provide knowledge and guidelines for selection, application, procurement, maintenance, and condition assessment and testing
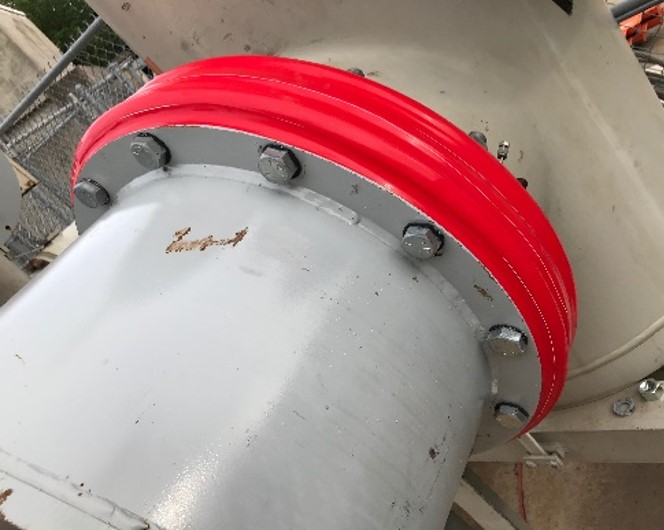
Novel SF6 Leak Sealing Techniques evaluates sealing materials and develops repair techniques for circuit breaker (CB) and gas insulated substations (GIS) that are:
-
Easy to apply, remove and reapply by utility personnel
-
Do not require specialized tools or clamps
-
Do not require de-pressurization
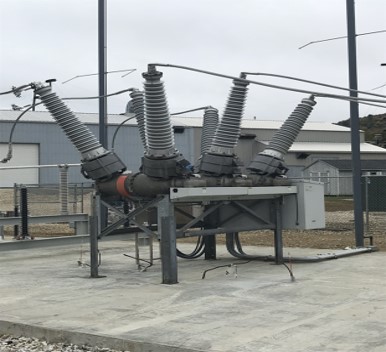
Effectiveness Assessment of Circuit Breaker Online Monitoring and Diagnostic Testing provides guidance for nonintrusive monitoring and diagnostic tests to support condition-based maintenance for interrupter arcing and main contacts.
Reference Information
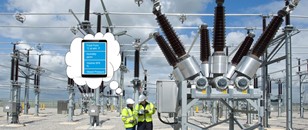
Circuit Breaker Mechanism Maintenance Guides Mechanism-specific maintenance supplements to serve as training tools for field personnel. Topics include proper disassembly, cleaning, lubrication, and reassembly. The library is updated with new guides every year.
Circuit Breaker Guidebook Development
EPRI is developing the Circuit Breaker Guidebook as a state of the art and
best practices guide to power circuit breaker operation, condition monitoring and diagnostics,
and maintenance. Ultimately, the Guidebook will provide utilities with a resource for circuit
breakers similar in scope to EPRI’s Copper Book for transformers.
The report presents the multiyear development approach, a proposed table of contents, drafts
of eight initial technical chapters, and the status of ongoing development
Videos
Circuit Breaker Lubrication Video Proper lubrication is essential to ensure reliable breaker operation and helps prevent premature failures and mis-operation. The video covers the importance of circuit breaker lubrication, selection and compatibility of lubricants and good practices to follow in the field.
Circuit Breaker Pump and Compressor Maintenance Video Utilities have diverse populations of circuit breaker compressors with different oils specified for different compressor types based on historical evolution. This video covers the importance of circuit breaker pump and compressor maintenance and provides information that can be use by maintenance personnel in inspecting, assessing and repairing circuit breaker pumps and compressors.